Free Air Delivery Explained
Understanding Your Numbers
Understanding Free Air Delivery (FAD): A Key Metric for Compressors
When you're dealing with compressors—whether in an industrial setting or for smaller-scale applications—understanding the concept of Free Air Delivery (FAD) is crucial. FAD refers to the actual volume of air delivered by a compressor at a specific pressure, adjusted to ambient conditions. In other words, it’s the measure of how much usable compressed air you’re getting out of your system. Let’s break down what FAD means, how it's measured, and why it matters.
What is Free Air Delivery (FAD)?
Free Air Delivery is a term used to describe the volume of compressed air a compressor can deliver, normalized to atmospheric conditions. Atmospheric pressure, humidity, and temperature can all affect air compression, and FAD accounts for these variables. The measurement is typically expressed in units like cubic meters per minute (m³/min) or liters per second (L/s).
When we talk about “free air,” we mean air that’s at the same temperature, pressure, and humidity as the surrounding environment, rather than air that has been compressed. The process of measuring FAD ensures that users understand the actual output of the compressor, rather than just the air compressed in the system.
How is FAD Measured?
Measuring FAD is more complex than simply observing how much air the compressor outputs. It requires a controlled environment where the output is measured and adjusted for standard atmospheric conditions (usually taken as 20°C temperature, 1 bar atmospheric pressure, and 0% relative humidity).
A simple test can be utilised to provide an estimate of FAD. This test is called a “Pump Up Test”
To carry out the test a known volume of down stream receiver capacity is required. The more accurate the known volume, the better the test. Ensure that any pipe work down stream of the receiver is isolated off and then allow the compressed air pressure within the receiver to drop lower than 1Bar below the cutout pressure of the compressor. Once at this pressure allow the compressor to come back on load and start pumping and then time how long it takes to increase receiver pressure by 1Bar. Ideally finishing the timing just below the cut out pressure. This can be repeated several times to get an average of actual time.
Once receiver volume is known and time value is known a simple calculation can be made to provide a FAD estimate for the compressor.
This information is helpful to determine if compressors are performing close to their name plate specification.
Why FAD Matters
It is the FAD and required system pressure that determine correct compressor sizing for an operation.
FAD provides a standardised figure for determining the volume of compressed air required for end use equipment and therefore determining compressor sizing requirements.
FAD is also required for determining piping network sizing and end use equipment tube sizing. Sizing of control valves and compressed air service units.
Conclusion
Free Air Delivery (FAD) is a fundamental concept in understanding compressor performance. It ensures that what you see on paper matches the actual performance you can expect in your environment. Whether you’re selecting a compressor for industrial machinery, manufacturing, or even more everyday tasks like powering pneumatic tools, knowing the FAD is essential for making the right choice. By focusing on this key metric, you can ensure your system is efficient, reliable, and meets your specific air requirements.
Having a solid grasp of FAD allows you to make more informed decisions, potentially saving both time and money while ensuring optimal system performance.
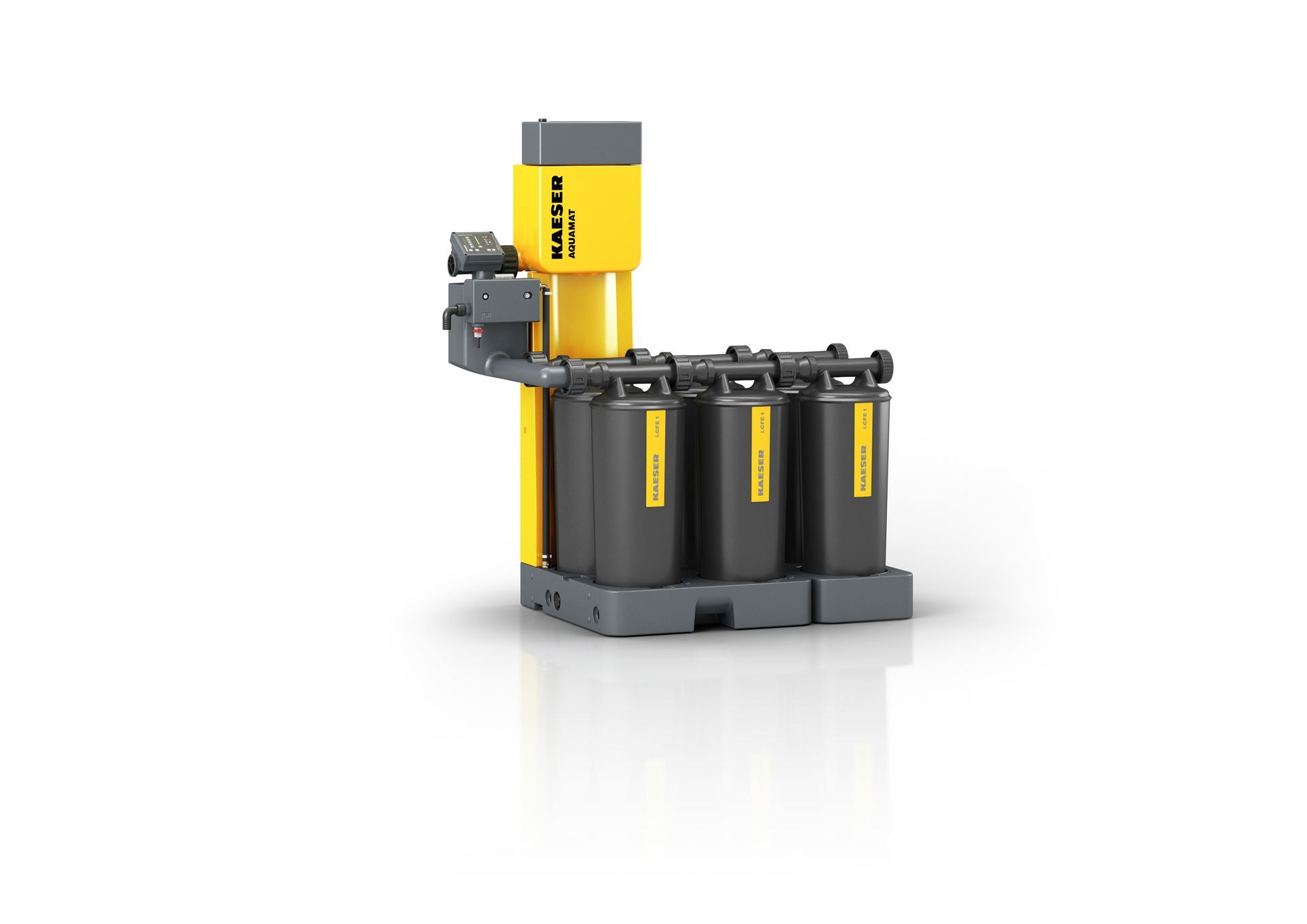
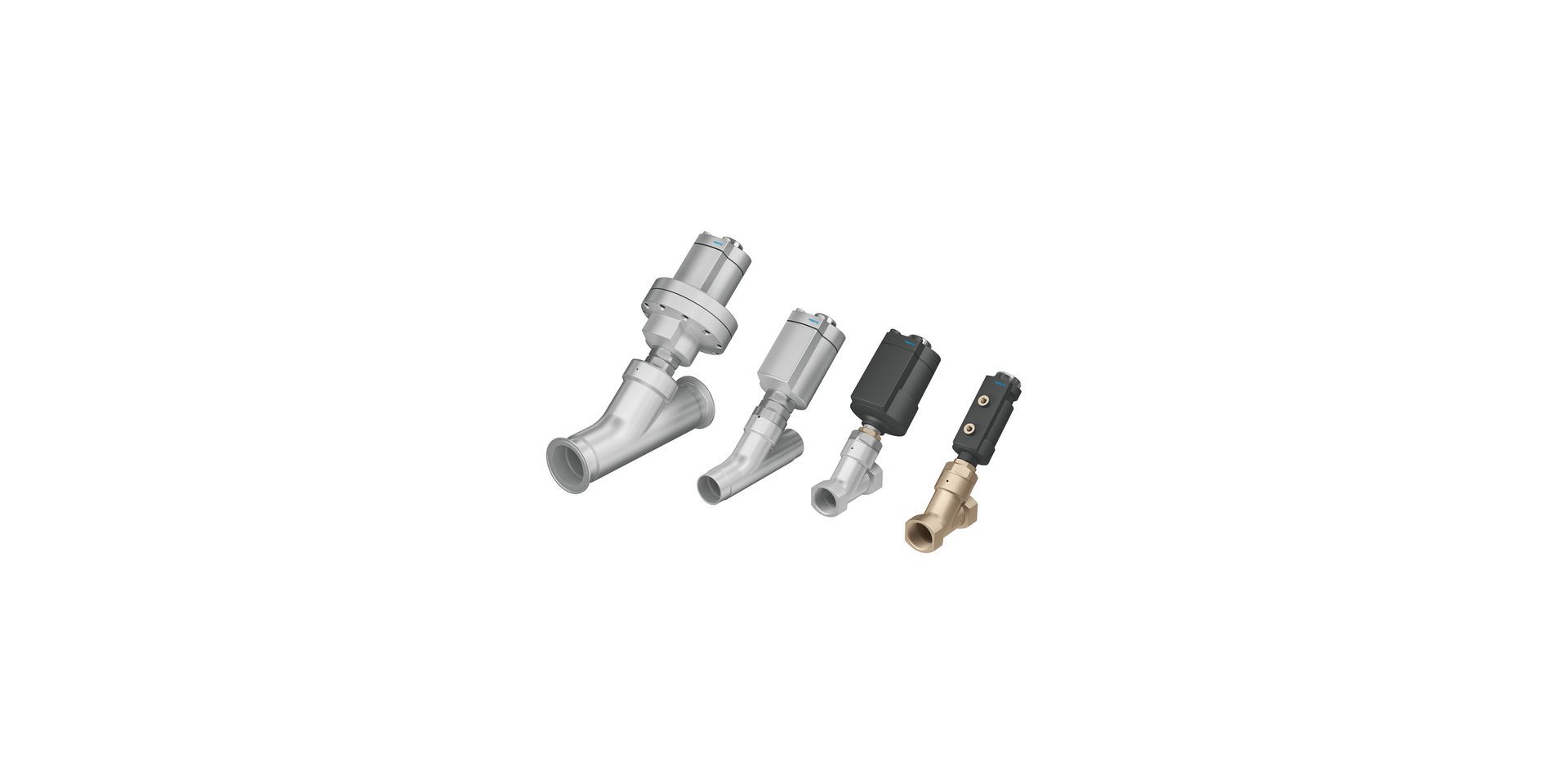
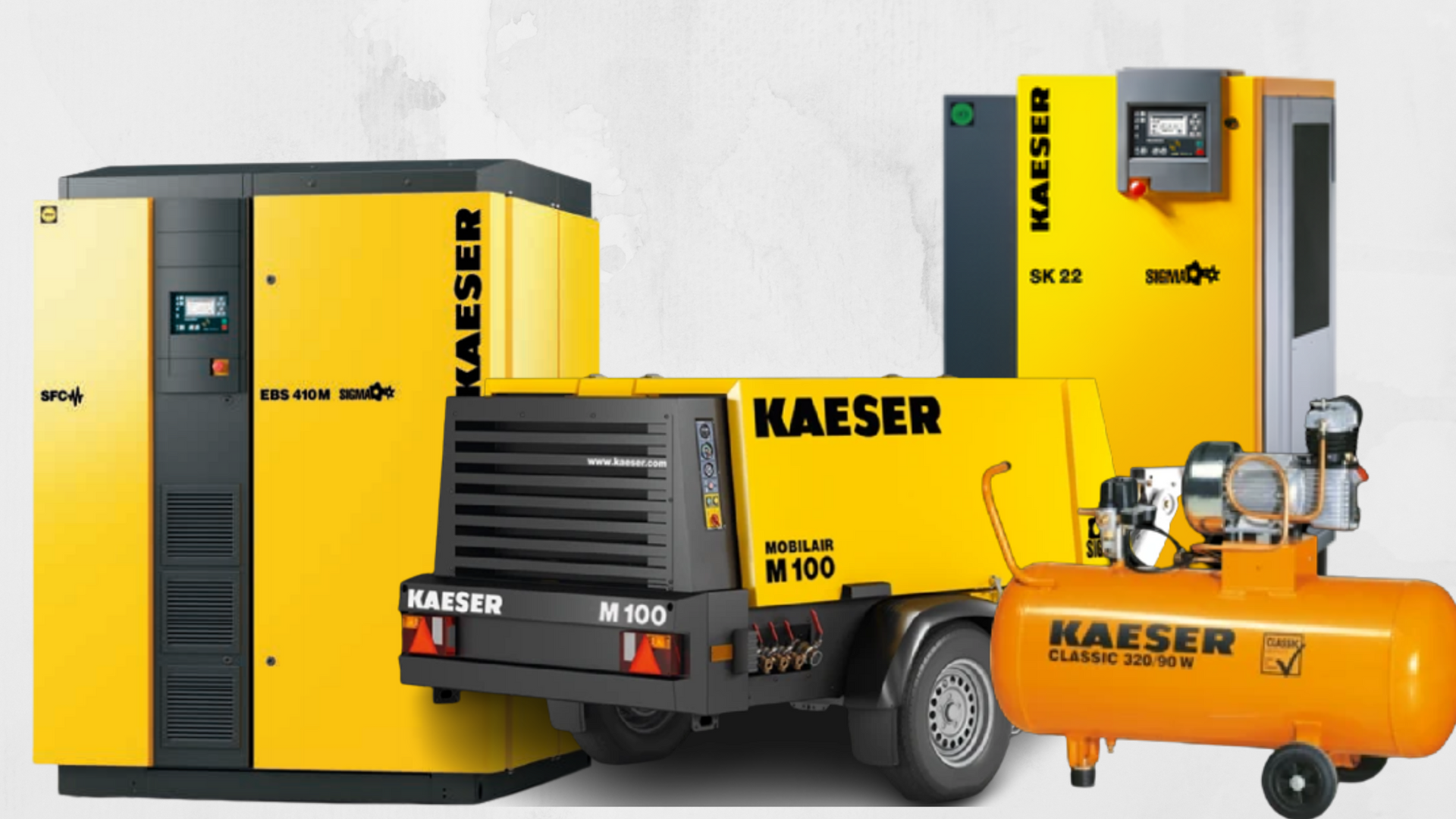
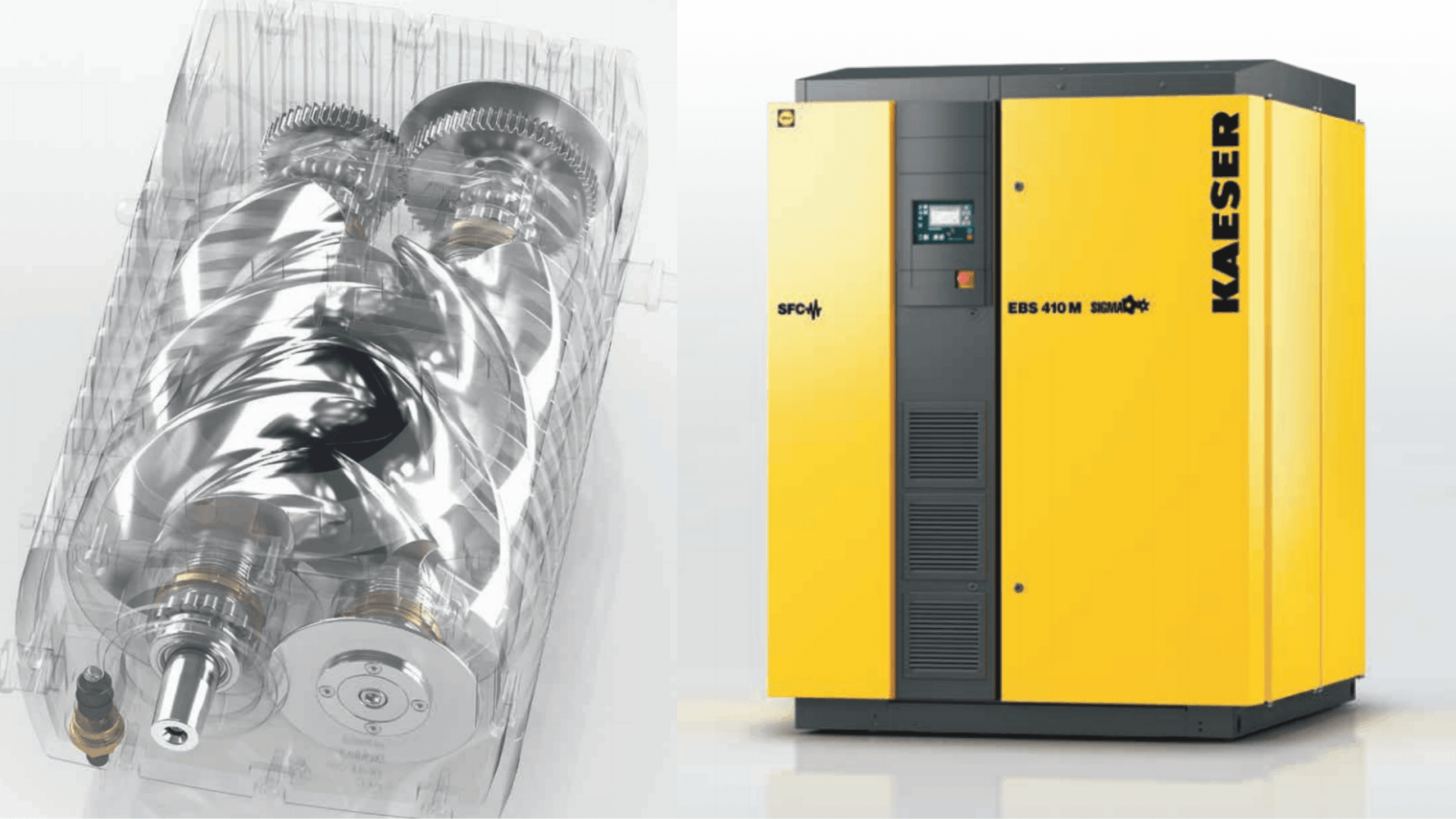
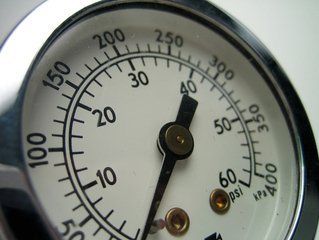