Streamlining Efficiency: The Multifaceted Role of Angle Seat Valves
Why Angle Seat Valves Are Essential for Modern Industrial Gas And Fluid Control
In industrial gas and fluid control systems, the selection of the right valve is critical for ensuring efficient, reliable, and safe operations. Among the various types of valves available, Festo's angle seat valves stand out for their unique design and versatility. But what exactly is the purpose of an angle seat valve? Let’s explore its key functions and the advantages it offers in various applications.
1.Efficient Flow Control
The primary purpose of an angle seat valve is to regulate the flow of fluids—liquids, gases, or steam—through a piping system. Its unique design, featuring an angled seat, creates a streamlined flow path that minimizes turbulence and pressure drop. Festo's range of VZXA Angle Seat Valves feature interchangeable actuator heads, so you can select the most efficient size and material for your application. This also means that if your demand changes, you can simply swap out the actuator head for a more suitable size as required. Angle seat valves are ideal for applications where maintaining high flow rates is crucial, such as in water treatment, chemical processing, and food and beverage production.
2. Space-Saving Design
Angle seat valves are designed to be compact, which makes them ideal for installations where space is limited. Their design allows them to fit into tight spaces without compromising performance, which is particularly useful in complex industrial systems where space optimization is a priority. The compact nature of angle seat valves also contributes to easier installation and integration into existing systems.
3. Rapid and Reliable Operation
In many industrial processes, the speed and reliability of valve operation are critical. The purpose of an angle seat valve is to provide fast and precise control over the opening and closing of the valve. This rapid response is essential in applications requiring quick adjustments to fluid flow, such as in automated manufacturing processes or systems where precise temperature control is needed. Testing of Festo's VZXA Angle Seat Valves showed they were able to perform a staggering 9 million switching cycles, compared to the 0.5 to 1 million that you'd expect with a ball valve. The reliable performance of angle seat valves ensures consistent operation with minimal downtime.
4. Versatile Application
Another important purpose of angle seat valves is their ability to function in a wide range of applications. They are versatile enough to handle different types of media, from aggressive chemicals to high-temperature steam, making them suitable for use in various industries. Festo's VZXA Angle Seat Valves are able to withstand temperatures ranging from -80°C to +230°C. Whether it’s controlling the flow of fluids in pharmaceutical production, food processing, or HVAC systems, angle seat valves offer the flexibility needed to meet diverse operational requirements.
5. Energy Efficiency
Energy efficiency is a key consideration in modern industrial systems, and angle seat valves play a significant role in this aspect. By providing a streamlined flow path and quick actuation, these valves reduce the amount of energy required to move fluids through the system. This not only lowers operational costs but also contributes to more sustainable and environmentally friendly operations.
6. Reduced Maintenance Needs
Maintenance is often a significant concern in industrial operations. The purpose of an angle seat valve includes minimizing maintenance requirements through its durable and straightforward design. With fewer moving parts and a construction that resists wear and tear, angle seat valves require less frequent maintenance, reducing downtime and overall costs associated with valve upkeep.
The purpose of an angle seat valve is multifaceted, serving to efficiently control fluid flow, save space, operate rapidly and reliably, and adapt to a wide range of applications. Additionally, angle seat valves contribute to energy efficiency, reduce maintenance needs, and enhance safety in industrial systems. These characteristics make angle seat valves an essential component in modern fluid control systems, offering superior performance and reliability across various industries.
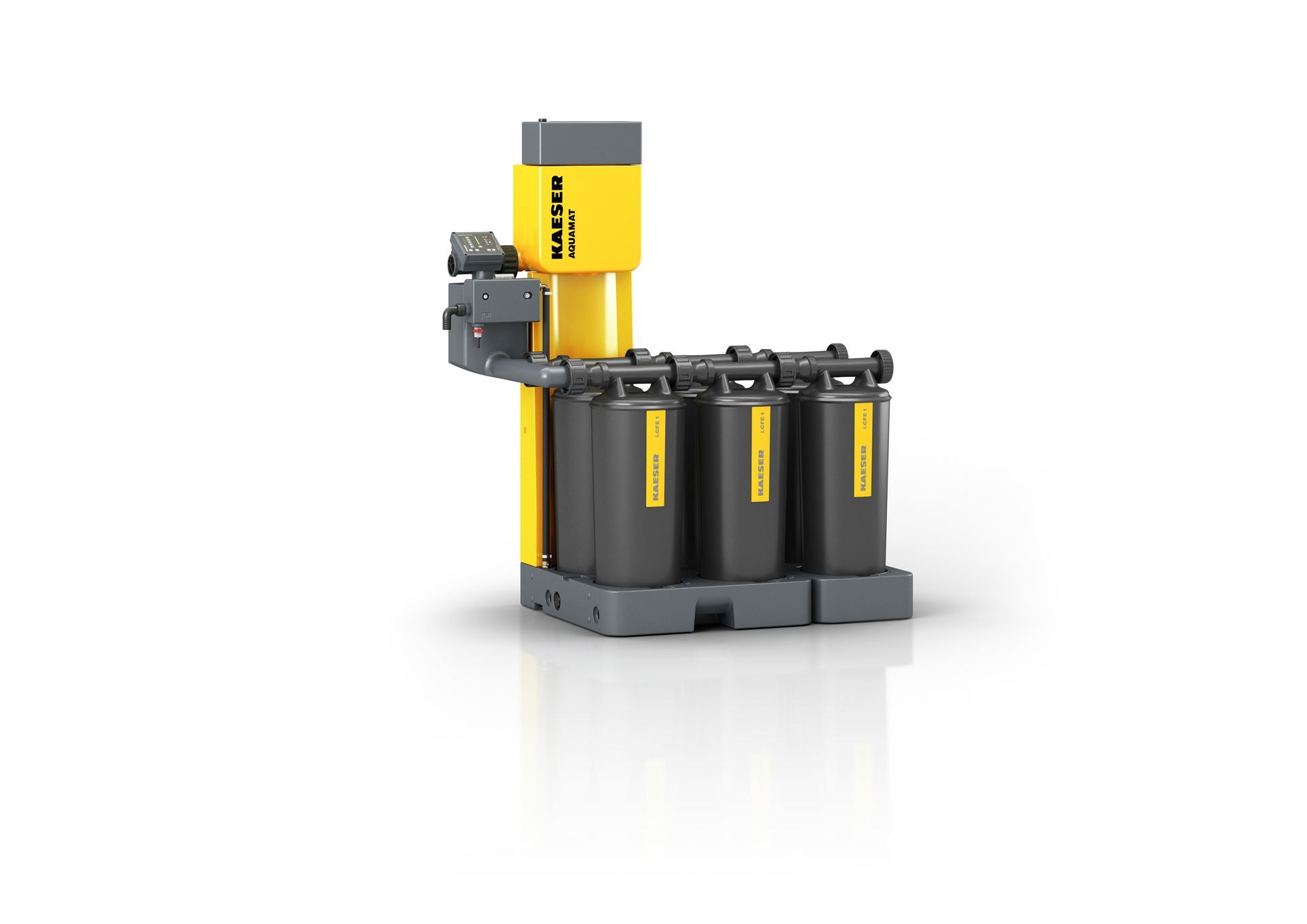
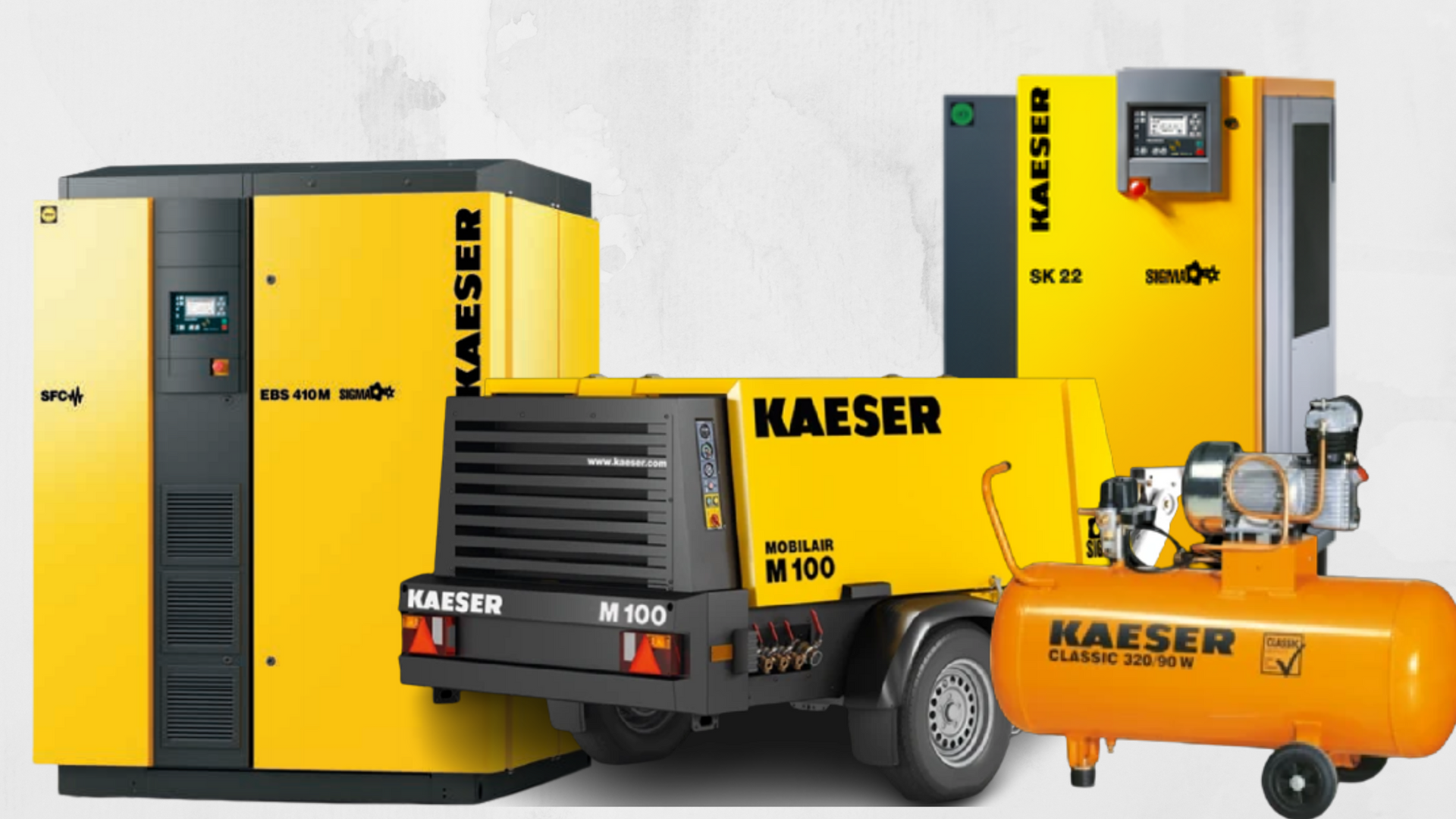
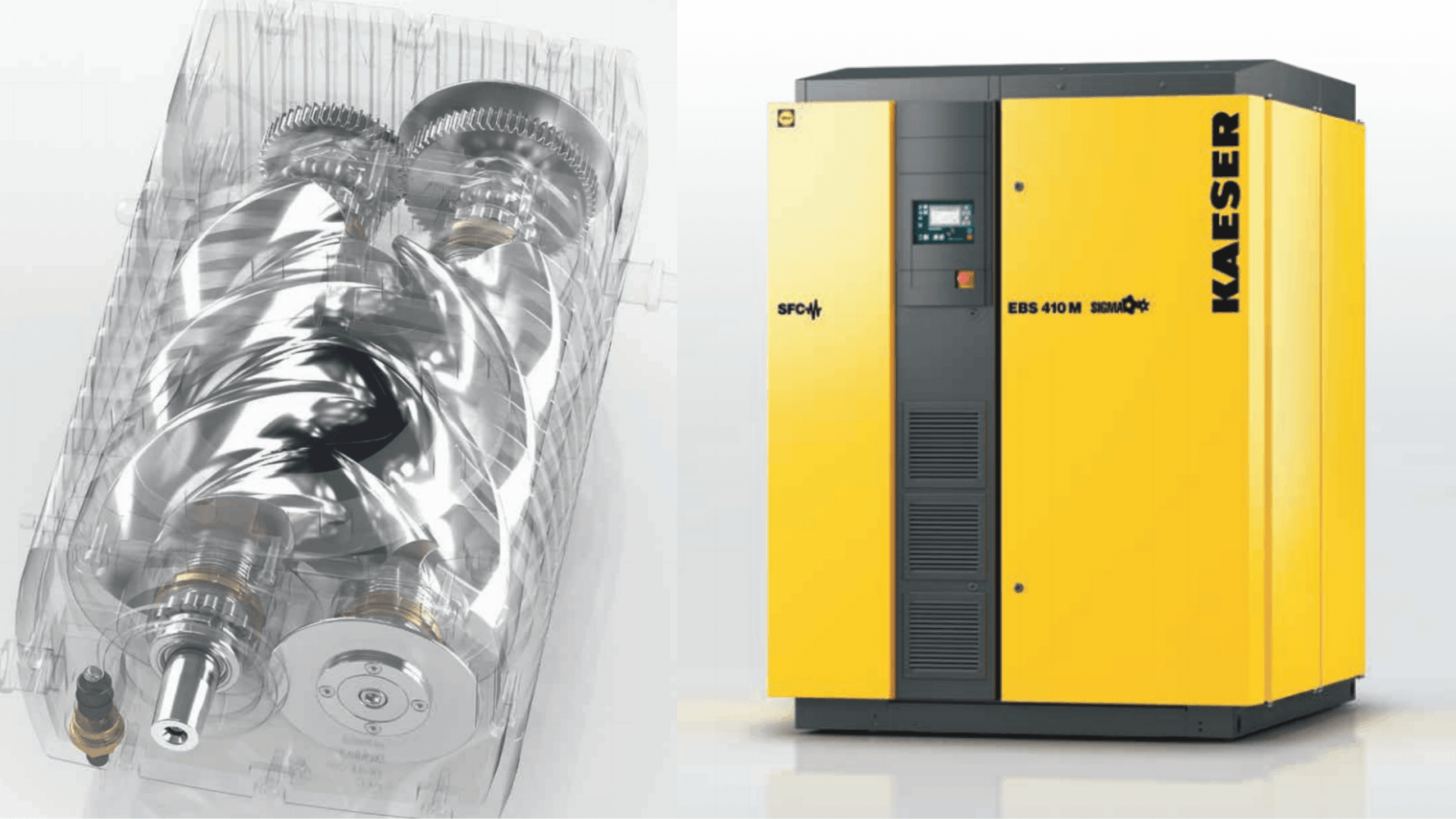
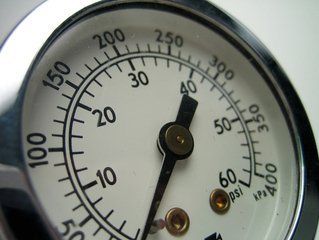